金币
UID176556
帖子
主题
积分25187
注册时间2014-6-6
最后登录1970-1-1
听众
性别保密
|
欢迎您注册蒲公英
您需要 登录 才可以下载或查看,没有帐号?立即注册
x
Baffle Options for Glass-Lined Reactors玻璃内衬反应釜的挡板选择
Sep 24, 2014 12:00:00 PM
Used in reaction and blending applications as well as material storage, agitated vessels are a key component in many chemical manufacturing processes. A baffle is an integral part of the vessel's mixing system that promotes better flow of fluids for maximum efficiency. Its primary function is to prevent the swirling in agitation by converting the swirling into a desired flow pattern. The next time you stir a cup of coffee, think of your spoon as an agitator. If you continue to stir in one direction a swirling motion is created in which little mixing actually takes place. The most effective mixing occurs after you stop stirring and allow your spoon to obstruct the flow that was created. Your spoon has become a baffle!
As with selecting the right agitator and desired flow pattern (axial flow for blending and solids suspension, radial flow for dispersion - see previous blog post for more on this topic) it is important to consider what kind of baffles to use and how to apply them in order to accomplish your process objectives.
Traditional Baffle Designs in Glass-Lined VesselsThe various types of flange-mounted, traditional baffles used in glass-lined vessels are depicted in the diagram below (Figure 1). Depending on your process objectives and the characteristics of your product, one baffle type may be more suitable than another for your application.
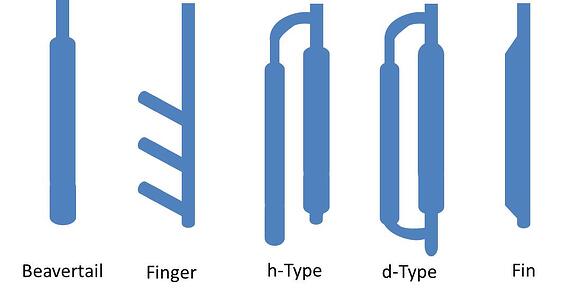
Figure 1. Traditional Baffle Configurations
The most commonly used design that offers superior performance for the majority of processes is the beavertail baffle (which, consequently, is the DDPS standard flange-mounted design). It can be conveniently installed through one of the standard nozzles on a reactor head, enabling easy, no-entry installation and removal. Additionally, the beavertail baffle encases a temperature sensing system and has proven to offer high performance even at low liquid levels.
DDPS conducted a test to compare the performance of the beavertail baffle with the finger and “h”-style baffles, as judged by agitator power draw and visual mixing capability. The graph below (figure 2) indicates that the beavertail is better than the other types at low levels and at least equivalent at higher levels. (Test conditions: 2,000 gallon SA reactor, GlasLock agitator with blades set at 60, down-pumping, 125 rpm in water.)

Figure 2. BeaverTail Baffle performance vs. Finger and "H"-Style Baffles
Beavertail baffles and other traditional units are specifically designed to hang from flanges in the vessel’s top head to ensure the integrity of the vessel lining. While this offers effective mixing, there are limitations and inefficiencies created by this arrangement. Traditional glass-lined reactors have employed a single baffle over multiple baffles mainly due to the challenge of attaching baffles to the reactor wall and encapsulating them with glass. Additionally, since mounting flanges are needed for process monitoring, insertion of cleaning devices, and the introduction of reactants, no more than two baffles are typically used due to the limited space in the head.
OptiMix Baffles The OptiMix design solves the issues faced by traditional baffle installations by welding the reactor wall prior to coating all steel surfaces with glass. (Before this design, wall-mounted baffles were only available on metallic reactors). This new configuration employs three glass-lined baffles, rather than the single baffle used in conventional glass-lined equipment. As a result, mixing times are reduced by approximately one-third through improvements in heat and mass transfer, solids suspension and distribution, gas dispersion and gas flow rates. The following graphs (figures 3a and 3b) illustrate the effect of 1, 2, 3 and 4 baffles on flow rates and mixing times, with 4 baffles yielding a negligible improvement over 3-baffle configurations.
Figure 3a  Figure 3b
There is an added benefit to matching the number of baffles to the number of agitation blades: each blade passes each of the three baffles simultaneously (as they are symmetrically positioned around the circumference of the vessel inner wall), canceling radial stresses and undesirable vibrations that would otherwise be incurred by the hub.
Customers who have installed and used OptiMix reactors for a period of time have compared their process output versus their previous conventional reactor and have shared their results:
- Improvements in mixing efficiency
- Elimination of the problem of solid particles flotation at the surface of the reaction medium
- The absence of a baffle flange mounted on the reactor head has freed room for a large nozzle for other usage.
- Design makes for easier cleaning between batch operations.
- The combination of these improvements has resulted in an overall productivity increase.
The design also allows OptiMix baffles to be retrofit during reglassing at about half the cost of a new reactor. After shot-blasting to remove all glass from the reactor interior, baffles are welded to the reactor wall, after which all interior surfaces are encapsulated with glass, giving the reactor a second life. And since the configuration of OptiMix reactors is similar to that of the company's traditional models, upgrades can be made with no modification to piping or connections.
DDPS has extended the range of the OptiMix reactor to provide improved heat transfer and reduced processing times. This new design, OptiMix-HE, circulates the thermal fluid contained in the half-coil reactor jacket through the baffles. This results in an increased heat transfer area up to 25% enabling more homogeneity, faster thermal management and shortened cycle times.
Benefits of BafflesWhether you choose a more conventional baffle design or decide to employ the OptiMix technology, there is an overwhelming advantage to using any kind of baffle in your process, though the level of efficiency and rates of improvement will vary. In addition to improved mixing, baffles can increase heat transfer and chemical reaction rates. Baffles also aid in decreasing vortex formation, increasing the power input of the agitator, and improving mechanical stability.
The following two videos demonstrate a side by side comparison of the advantages baffles have on mixing. The vessels feature identical parameters to one another except the vessel on the right contains three wall-mounted baffles and the vessel on the left has no baffling system.
In the first video the unbaffled vessel is not as efficient in dispersing solids whereas the presence of baffles produces axial flow in combination with pitch-blade impeller, resulting in the uniform distribution of solid particles. The second video clearly shows the dramatic effect the OptiMix baffles have on reducing the vortex that is created at the surface level of the liquid at the agitator as well as the improved cleanability that is created due to a decrease in product splashing on the vessel wall.
Video 1
Video 2
Often overlooked and taken for granted as a standard piece of equipment, baffles prove to be a critical component to a glass-lined vessel’s mixing system, as you can see from all the different choices available and the huge impact they have on mixing. Identifying the right one to match your defined process objectives is important to ensure your process runs at maximum performance. If you have a new process, problems with your current mixing system, or are simply looking to optimize the performance of an existing process, then we can help! By filling out and submitting the Agitation Simulation Questionnaire, we’ll be able to provide you with a simulation to demonstrate how your process can be improved. To find out more on our OptiMix baffles and learn about the other enhancements available for glass-lined reactors, watch our animation “Optimizing the Glass-Lined Reactor”
|
|